Elektrifizierung und Automatisierung haben sich in China rasant entwickelt.Kompaktleistungsschalter (MCCBs) werden aufgrund ihrer guten Überlast- und Kurzschlussschutzfunktionen häufig eingesetzt.
1.Hintergrund:
Elektrifizierung und Automatisierung haben sich in China rasant entwickelt.Kompaktleistungsschalter (MCCBs) werden aufgrund ihrer guten Überlast- und Kurzschlussschutzfunktionen häufig eingesetzt. MCCBs, als die grundlegendsten Schutzgeräte, zeichnen sich durch eine umfangreiche Anwendung, eine breite Palette von Sorten und eine kompakte und komplizierte Struktur aus. In der Vergangenheit hielten es Konstrukteure und Hersteller von Elektrogeräten oft für notwendig, Prototypenteile durch Silikonbeschichtungsbearbeitung und CNC-Bearbeitung herzustellen und Verifizierungen und Tests in der Entwurfs- und Entwicklungsphase neuer Produkte durchzuführen, was einen langen Verarbeitungszyklus und hohe Kosten erfordern und zu einem großen Problem werden würde, wenn jedes Jahr Dutzende oder Hunderte neuer Produkte entwickelt werden müssten. Im Folgenden wird ein Fall mit einem Endkunden von TPM3D dargestellt.
2.Kundenprofil:
Der Kunde ist ein weltweit renommierter Anbieter von intelligenten Energielösungen, und seine Produkte umfassen Stromverteiler, Terminalgeräte, Motorsteuerungs- und Schutzgeräte, industrielle Automatisierung usw. Mit einem Jahresumsatz von über 80 Milliarden RMB ist das Unternehmen in mehr als 140 Ländern und Regionen tätig. Dieser Kunde kombiniert das Lasersintersystem TPM3D P360 mit PPS für seine Forschung und Entwicklung und Testproduktion verschiedener elektrischer Niederspannungsgeräte.
3. Produktentwicklung:
Der Kunde entwickelt und produziert jährlich mehr als 10.000 neue Elektroprodukte. Zu den Hauptprodukten, die derzeit mit TPM3D P360 gedruckt werden, gehören Gehäuse für Kompaktleistungsschalter und andere Strukturteile.
Nachdem das Muster gedruckt wurde, führt der Kunde eine Montageüberprüfung und Funktionstests durch. Die Genauigkeit der Montageüberprüfung ist erforderlich, um ±0,2 mm zu erreichen. Die Funktionstests umfassen hauptsächlich: Festigkeitstest, Langzeitverzögerungstest, Isolationstest usw. Das verwendete Material besteht zu 30% aus glasperlenverstärktem Nylon 12 (Precimid1172Pro GF30) von TMP3D, das sich durch hervorragende Festigkeit und Schlagzähigkeit auszeichnet. Nach Angaben des Kunden können die Materialien die Testanforderungen in Bezug auf mechanische Eigenschaften und Isolierung erfüllen. Darüber hinaus erreicht die thermische Verformungstemperatur des Materials bis zu 184,4 ° C, und die bedruckten Gehäuse können 4 Stunden lang ohne Verformung in einem Thermostat bei 80 ° C getestet werden, was die Anforderungen der Langzeitverzögerungsprüfung erfüllt. Insgesamt liegen die mit SLS-Technologie bedruckten Gehäuseleistungsschalter auf Augenhöhe mit herkömmlichen Spritzgussteilen.
4.Umweltfreundlich:
Beim Kauf des P360-Lasersintersystems konfigurierte der Kunde auch eine Parts & Powder Processing Station (PPS), die 2018 von TPM3D, der ersten in Asien, eingeführt wurde, integriert Teilereinigung, Pulverrecycling, Mischen, Füttern und Pulversammeln, löste die Probleme wie Zeitverschwendung, Umweltverschmutzung und Sicherheit im Arbeitsbetrieb. PPS hat die nationale Norm für staubexplosionsgeschützte Zone 22 und die internationale CE-Zertifizierung bestanden und eine hohe Anerkennung für seine bessere Leistung bei der Gewährleistung der Benutzersicherheit erhalten.
5.Kostensenkung und Effizienzsteigerung:
Vor der Einführung des SLS 3D-Drucksystems entschied sich der Kunde für CNC-Bearbeitung oder ausgelagerte Silikonbeschichtungsbearbeitung, die mindestens 5-6 Tage dauerte, um die Testteile zu erhalten. Nachdem die Lasersinteranlage P360 in Produktion genommen wurde, konnten bereits nach 48 Stunden Proben beschafft und getestet werden, was zu einer Zeitersparnis von mehr als 60% führte. In der Vergangenheit kostete die ausgelagerte Fallbearbeitung etwa 4.000 RMB / Set. Mit der SLS 3D-Drucktechnologie können die Kosten unter RMB 700 / Satz kontrolliert werden, was einer Reduzierung um mehr als 80% entspricht. Bei einer hohen Auslastungsrate können die Geräte des Kunden derzeit durchschnittlich 2-3 volle Kammern pro Woche drucken. Darüber hinaus kann es nach Angaben des Kunden etwa 700.000 RMB pro Jahr einsparen, wodurch die Kosten besser gesenkt und die Effizienz verbessert werden.
Vergleich von Kosten und Zyklus zwischen traditionellem Verfahren und SLS-3D-Druckverfahren:
"Das P360-System von TPM3D ist bequem und schnell. PPS reduziert manuelle Eingriffe und erreicht gleichzeitig eine hohe Verarbeitungseffizienz von Teilen und Pulver. Die Lösung spart Zeit und Kosten und sorgt für Ordnung und Sicherheit der Umwelt."
——Feedback vom Kunden
Elektrifizierung und Automatisierung haben sich in China rasant entwickelt.Kompaktleistungsschalter (MCCBs) werden aufgrund ihrer guten Überlast- und Kurzschlussschutzfunktionen häufig eingesetzt. MCCBs, als die grundlegendsten Schutzgeräte, zeichnen sich durch eine umfangreiche Anwendung, eine breite Palette von Sorten und eine kompakte und komplizierte Struktur aus. In der Vergangenheit hielten es Konstrukteure und Hersteller von Elektrogeräten oft für notwendig, Prototypenteile durch Silikonbeschichtungsbearbeitung und CNC-Bearbeitung herzustellen und Verifizierungen und Tests in der Entwurfs- und Entwicklungsphase neuer Produkte durchzuführen, was einen langen Verarbeitungszyklus und hohe Kosten erfordern und zu einem großen Problem werden würde, wenn jedes Jahr Dutzende oder Hunderte neuer Produkte entwickelt werden müssten. Im Folgenden wird ein Fall mit einem Endkunden von TPM3D dargestellt.

Eine Art Kompaktleistungsschalter
2.Kundenprofil:
Der Kunde ist ein weltweit renommierter Anbieter von intelligenten Energielösungen, und seine Produkte umfassen Stromverteiler, Terminalgeräte, Motorsteuerungs- und Schutzgeräte, industrielle Automatisierung usw. Mit einem Jahresumsatz von über 80 Milliarden RMB ist das Unternehmen in mehr als 140 Ländern und Regionen tätig. Dieser Kunde kombiniert das Lasersintersystem TPM3D P360 mit PPS für seine Forschung und Entwicklung und Testproduktion verschiedener elektrischer Niederspannungsgeräte.
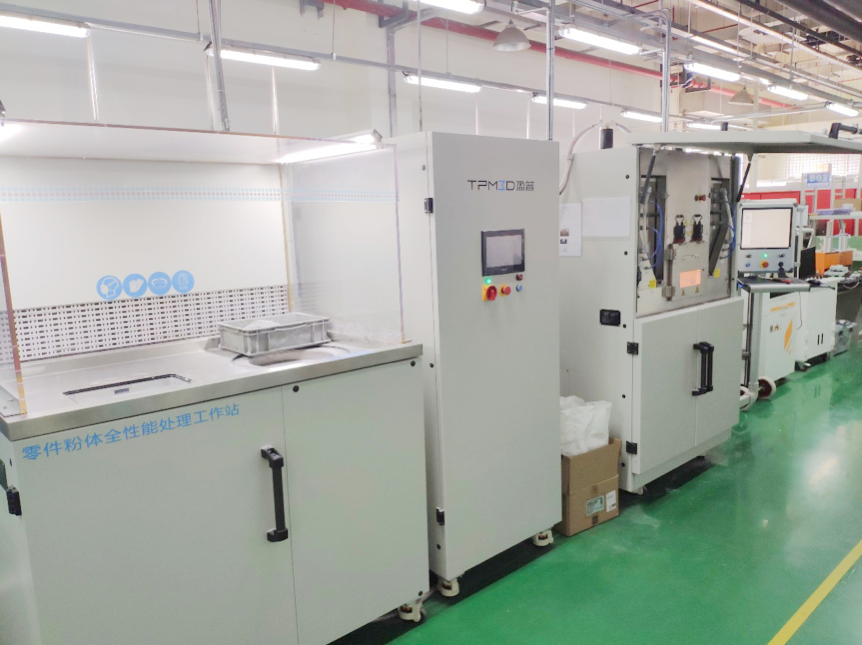
TPM3D P360 Lasersinteranlage +PPS
3. Produktentwicklung:
Der Kunde entwickelt und produziert jährlich mehr als 10.000 neue Elektroprodukte. Zu den Hauptprodukten, die derzeit mit TPM3D P360 gedruckt werden, gehören Gehäuse für Kompaktleistungsschalter und andere Strukturteile.

von SLS Technology entwickelter Kompaktleistungsschalter
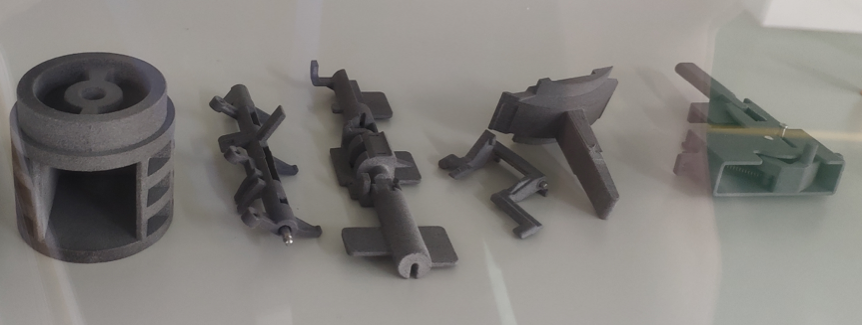
Sonstige Bauteile
Nachdem das Muster gedruckt wurde, führt der Kunde eine Montageüberprüfung und Funktionstests durch. Die Genauigkeit der Montageüberprüfung ist erforderlich, um ±0,2 mm zu erreichen. Die Funktionstests umfassen hauptsächlich: Festigkeitstest, Langzeitverzögerungstest, Isolationstest usw. Das verwendete Material besteht zu 30% aus glasperlenverstärktem Nylon 12 (Precimid1172Pro GF30) von TMP3D, das sich durch hervorragende Festigkeit und Schlagzähigkeit auszeichnet. Nach Angaben des Kunden können die Materialien die Testanforderungen in Bezug auf mechanische Eigenschaften und Isolierung erfüllen. Darüber hinaus erreicht die thermische Verformungstemperatur des Materials bis zu 184,4 ° C, und die bedruckten Gehäuse können 4 Stunden lang ohne Verformung in einem Thermostat bei 80 ° C getestet werden, was die Anforderungen der Langzeitverzögerungsprüfung erfüllt. Insgesamt liegen die mit SLS-Technologie bedruckten Gehäuseleistungsschalter auf Augenhöhe mit herkömmlichen Spritzgussteilen.
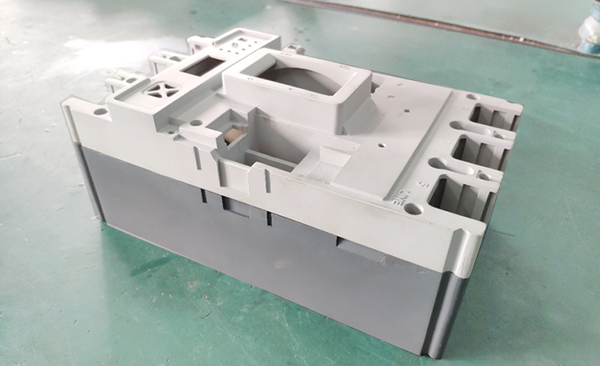
Montage-Verifizierung
4.Umweltfreundlich:
Beim Kauf des P360-Lasersintersystems konfigurierte der Kunde auch eine Parts & Powder Processing Station (PPS), die 2018 von TPM3D, der ersten in Asien, eingeführt wurde, integriert Teilereinigung, Pulverrecycling, Mischen, Füttern und Pulversammeln, löste die Probleme wie Zeitverschwendung, Umweltverschmutzung und Sicherheit im Arbeitsbetrieb. PPS hat die nationale Norm für staubexplosionsgeschützte Zone 22 und die internationale CE-Zertifizierung bestanden und eine hohe Anerkennung für seine bessere Leistung bei der Gewährleistung der Benutzersicherheit erhalten.
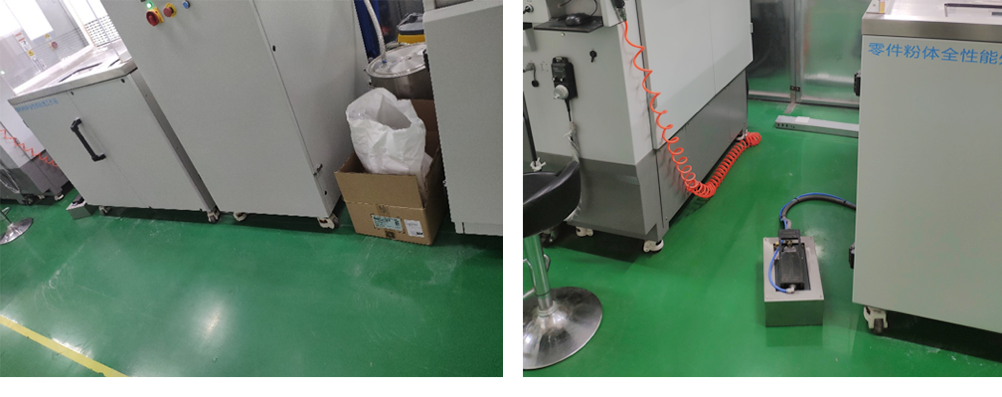
saubere und ordentliche Umgebung
5.Kostensenkung und Effizienzsteigerung:
Vor der Einführung des SLS 3D-Drucksystems entschied sich der Kunde für CNC-Bearbeitung oder ausgelagerte Silikonbeschichtungsbearbeitung, die mindestens 5-6 Tage dauerte, um die Testteile zu erhalten. Nachdem die Lasersinteranlage P360 in Produktion genommen wurde, konnten bereits nach 48 Stunden Proben beschafft und getestet werden, was zu einer Zeitersparnis von mehr als 60% führte. In der Vergangenheit kostete die ausgelagerte Fallbearbeitung etwa 4.000 RMB / Set. Mit der SLS 3D-Drucktechnologie können die Kosten unter RMB 700 / Satz kontrolliert werden, was einer Reduzierung um mehr als 80% entspricht. Bei einer hohen Auslastungsrate können die Geräte des Kunden derzeit durchschnittlich 2-3 volle Kammern pro Woche drucken. Darüber hinaus kann es nach Angaben des Kunden etwa 700.000 RMB pro Jahr einsparen, wodurch die Kosten besser gesenkt und die Effizienz verbessert werden.
Vergleich von Kosten und Zyklus zwischen traditionellem Verfahren und SLS-3D-Druckverfahren:
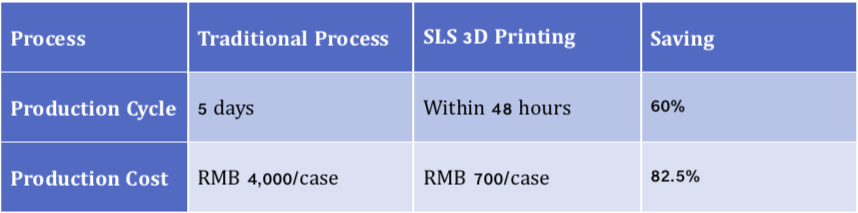
"Das P360-System von TPM3D ist bequem und schnell. PPS reduziert manuelle Eingriffe und erreicht gleichzeitig eine hohe Verarbeitungseffizienz von Teilen und Pulver. Die Lösung spart Zeit und Kosten und sorgt für Ordnung und Sicherheit der Umwelt."
——Feedback vom Kunden